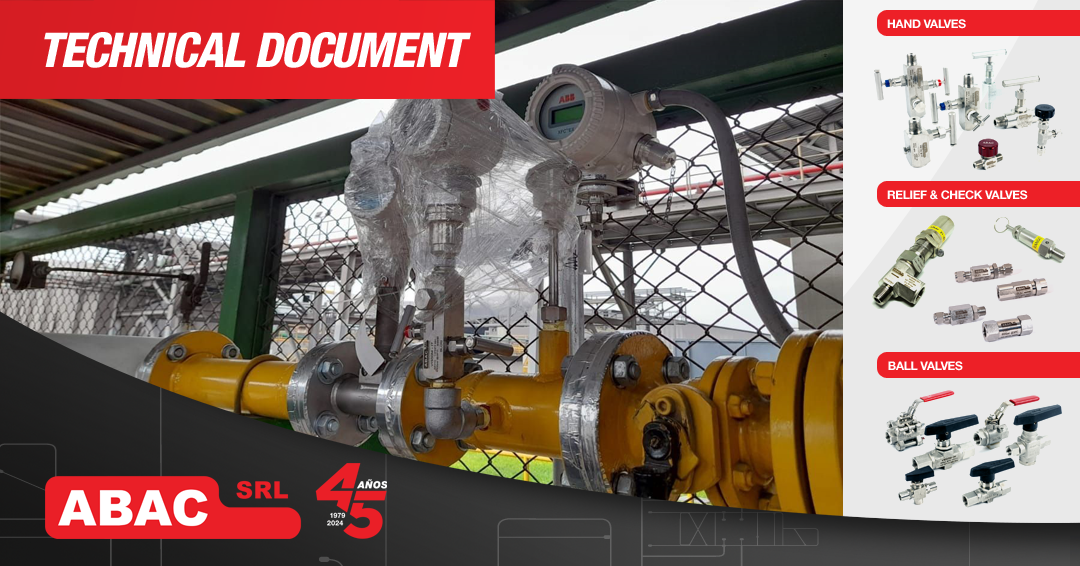
The choice of valves is an important part of the design and maintenance of industrial, piping and instrumentation systems. Without the right valve for a specific application, we could face inadequate or poor fluid system performance and unavoidable safety risks.
Typically, valves are chosen during the initial design of the system. Throughout the life of the system, maintenance technicians typically replace valves and most other components with others of the same type, according to specifications. This makes it even more important to choose the right valve from the start, and can help avoid the need to change the valve prematurely.
For proper valve selection, designers and technicians can apply the STAMPED method, which takes into account size, temperature, application, fluid, pressure, end connection ends, and delivery. All this according to its acronym in English: Size, Temperature, Application, Material/Media, Pressure, Ends and Delivery.
Let’s see how to apply the STAMPED method to the design of a fluid system:
S: Size
The size of the valve determines its flow capacity and must correspond to the desired or required flow. The manufacturer should provide a flow coefficient (CV), which indicates the relationship between the pressure drop across the valve and the corresponding flow rate. The CV is the amount of water in gallons per minute that will flow through a valve with a pressure drop of 1 psi and a temperature of 60°F.
The larger the orifice, the greater the potential flow capacity. The orifices of different types of valves can vary considerably, for example a ball valve will offer minimal resistance to flow, but a needle valve can restrict or reduce flow.
T: Temperature
Take into account the temperatures at which the valve will operate. This includes both the system fluid temperature and the working environment temperature.
Think about temperature fluctuations that can cause closure materials to expand and contract. Metal components can also lose strength at higher temperatures, reducing pressure ratings.
A: Application
Take into account what the valve has to do in the system. Open or close the flow? Regulate the flow level? Control flow direction? Protect the system from excess pressure?
If the intention is to reduce or regulate the flow, the best option would be a needle or regulation valve. Ball valves should not be used to regulate or reduce flow. They are designed to be used in a fully open or closed position.
M: Material/Media
The process fluid within the system must also be carefully analyzed while seeking to select the correct valve. Ensure that the system fluid is compatible with the materials of construction of the valve bodies, seats, plugs, and other softer materials.
As with temperature, where the valve will be put into service (environmental conditions) must also be considered.
P: Pressure
Pressure is another important consideration in your valve selection, for both contexts in which the term is used:
Service Pressure: The normal operating pressure of the system.
Design pressure: The maximum pressure limit is provided by the valve manufacturer. Never exceed the design pressure of any fluid system component (except under controlled test conditions).
E: Ends
Valves are supplied with a variety of different end connections. These can be of the double ferrule type (for tubing), conical/cylindrical threads, pipe flanges, welded ends, etc.
Ensure that end connections are appropriate for the system pressure and temperature, and are the correct size. Proper end connection can simplify installation and prevent additional leak points.
D: Delivery
On-time delivery and reliable supply are as important to keeping the fluid system operational and efficient as any other factor.
As we have seen, valve selection is an integral part of designing safe and efficient fluid systems. For more information, access our catalogs and/or contact us at ventas@abac.com.ar.