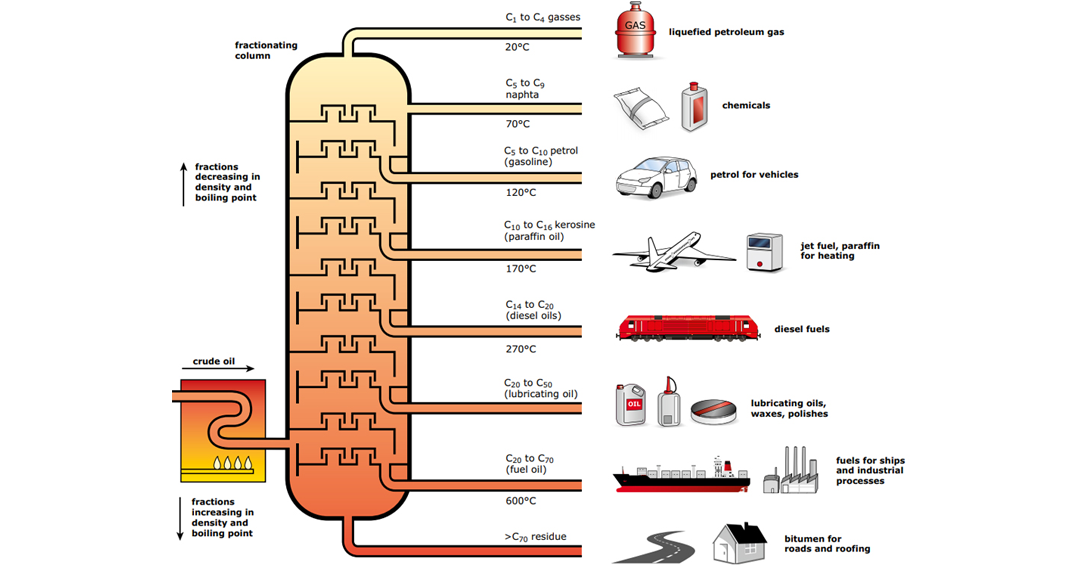
Petroleum refining is a complex process used to separate the various hydrocarbon fractions from crude oil (unprocessed oil). Hydrocarbons contain a lot of energy. They are molecules that contain hydrogen and carbon, and carbon comes in various lengths and structures.
Oil refineries operate 24 hours a day to convert crude oil into useful derivatives. Oil is separated into several fractions used for different purposes. Some fractions have to undergo thermal and chemical treatments to convert them into final products.
In any refining process there are common phases that allow obtaining crude oil derivatives to be possible. Before the first phase, there may be a previous one in which the oil is preheated for subsequent treatment.
Separation Phase: Distillation or absorption is used to desalt and dehydrate the crude oil so that when it is heated it is easier for its molecules to separate.
Cracking Phase: Using a heat source, the oil is heated to the desired boiling point so that the large chains of hydrocarbon molecules are broken into smaller molecules.
Fractionation Phase: The crude oil, already heated and ready for treatment, goes to the fractionation or distillation columns, where very high temperatures are applied. The derivative products and lighter components such as gas are concentrated in the highest part of the column. The heaviest ones are at the bottom.
Extraction Phase: After treatment in the column, the product is extracted through the upper part (for the lightest components), the lower part (for those heavy components) and the sides (for the intermediate components).
Post extraction, it is usual to store the petroleum product after refining. Before, it is most likely that they have passed through a condensation unit to additionally cool the product and reduce the temperature derived from the process.
What products arise from petroleum refining?
In the fractionation column, as we have explained, different products arise depending on the boiling point and density after heating the crude oil. Not only fuel derived from petroleum is produced, there are many other products that arise after this process:
• Liquefied Petroleum Gas is one of the least dense components and barely boils at 20°C (68°F), making it one of the lightest petroleum derivatives.
• Chemical Products also require less temperature to boil, achieving their release to the market after a new similar treatment until the final component needed is found.
• Gasoline -or Naphtha- for Vehicles arises at approximately 120°C (248°F) boiling point and within the fractionation tower it is in the upper zone. After further treatment, it will give rise to 95 or 98 gasoline.
• The next derivative that arises in the fractionation tower is Jet Fuel, due to the presence of kerosene as a previous product. Also Paraffin and Heating Oil.
• In the middle of the tower, Diesel Fuels appear, so here you can find one of the big differences between gasoline or diesel. In the oil refining process, they arise at different boiling points and their density is completely different.
• One of the densest products is the one that will later be used for Oils, different types of Lubricants or Waxes.
• The last of the fuels derived from petroleum through refinement is Industrial or Boat Fuel, which requires a temperature greater than 600°C (1112°F) to boil.
• Finally, in the lower part of the fractionation tower the waste appears with which Bitumen will later be made to pave or to make the roofs of the homes.
In this oil refining process, ABAC is present with its valves and manifolds for pressure instruments and other components for fluid control.
Photo: www.oiltanking.com